快速精通软件教程含系统化结构>>> (内含193处实战经验、106处小技巧分享,共270集)
请登录您的授权账号!本站目前可免费注册成为会员!
注册审批或者升级会员请联系站长!QQ:2621139966 微信:Creo2077
重要知识点笔记:
- 模具布局常用于模具设计。
- 模具布局功能主要用于模具设计,可以定位模具型腔,设计模架,并导入注射成型机,方便模具工程师进行操作。
- 该功能可以进行模具开模分析,帮助工程师了解模具的运作情况,从而优化设计,提高生产效率。
- 模具布局还支持快速设置流道水线和顶杆孔,这些都是模具设计中非常重要的环节,可以提高模具的冷却效果和顶出效果。
- 对于产品结构设计人员来说,最重要的是保证产品能够正常脱模,也就是说产品需要有适当的脱模斜度,这是产品设计的基础。
- 结构设计应尽量简单化,因为结构越简单,模具就越简单,模具成本也就越低,这对于降低生产成本非常重要。
思考:
- 产品结构设计人员需要掌握哪些模具相关的知识?
- UG软件中模具布局功能在高版本和低版本中有什么区别?
免费系统化曲面教程>>>(思路细节精讲)
联系站长; QQ:2621139966 微信:Creo2077 学习交流群; QQ1群:602849358 QQ2群:916477208
关于视频:
视频编号<139> 视频已为您加入隐藏水印
学习遇到问题欢迎加群一起学习讨论!
一.关于模流分析
1.关于 PTC Creo Mold Analysis
关于 PTC Creo Mold Analysis:
Creo Mold Analysis (CMA) 是注射成型模拟应用程序。可以使用 CMA 来校验零件设计的制造可行性,以避免出现成型方面的缺陷。最常见的成型问题是型腔填充不完全、熔接痕位置不当以及壁厚不合适。
可使用独特的网格自动剖分功能来准备可在更短时间内完成分析的模型。此外,CMA 将根据可能的熔接痕位置、困气位置以及所需的锁模力提供产品设计方面的建议。
流动行为
型腔填充是注射成型过程中的一个重要步骤。在填充过程中,熔体前沿以三维瞬态形式移动。非牛顿流体流动和耦合热传递可导致填充过程中出现问题。在填充过程中,可能会因以下原因产生产品缺陷:
•设计缺陷
•工艺不当
•材料不当
塑料熔体往往容易朝型腔中阻力最小的方向流动。下图显示了填充过程中的流动行为。箭头用于指示流动方向。塑料熔体向前的速度越快,则表示流动的阻力越小。
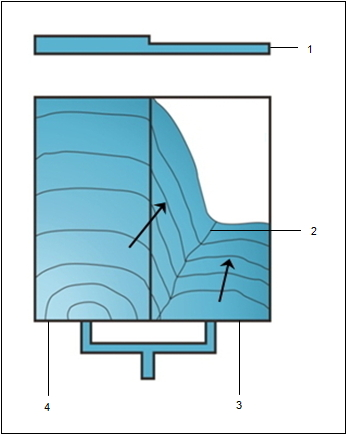
1.厚度分布
2.熔接痕
3.流动阻力较大区域
4.流动阻力较小区域
塑料熔体的黏度用于度量流动阻力。高黏度将增大流动阻力。因此,应仔细分析影响塑料熔体黏度的因素。影响黏度的因素包括局部温度、热传递率、剪切速率和零件厚度。这些因素均可用于优化填充过程。
零件厚度是最重要的因素。塑料零件较厚的部分将产生较小的流动阻力,因而会使塑料熔体更易于流动。此外,因为热塑性塑料的热导率不佳,所以较厚的部分难以导热。因此,越厚的部分温度就越高。同样,塑料熔体越薄的部分温度就越低,且流动阻力也越大。
在填充过程中,应注意以下内容:
•因填充不完全导致的短射情况
•是否存在迟滞
•出现的熔接痕和困气及其所在位置
•因多浇口导致的流动不平衡行为
•填充过程中的温度分布和变化情况
•主流道压力和锁模力的大小
应检查以下由于熔体前沿的细节所导致的问题:
•针对流动性检查填充模式。
•检查型腔或短射的填充不完全情况。
•检查流动不平衡情况。
•确定熔接痕和困气的位置。
•检查每个浇口的流动贡献度。
•检查浇口位置是否正确,以便可以平衡流动和消除熔接痕。
2.关于模具分析工作流
关于模具分析工作流:
1.在 Creo Parametric 中打开一个 .prt 文件。
2.单击“应用程序”(Applications) > “模具分析”(Mold Analysis)。“模具分析”(Mold Analysis) 选项卡随即打开。
3.从“材料库”(Material library) 中选择一种材料。如果库中没有此材料,则可修改某个现有材料的属性。
4.在模型中添加浇口。可手动或自动添加浇口位置。也可编辑浇口直径。
5.设置分析的加工条件。可通过选择附加模拟的选项来估计冷却时间和缩痕。基于分析所需的精度选择网格元素大小。
6.运行分析。可通过更改模型的材料、浇口和加工条件来执行多个分析。
7.查看分析结果。从“分析设置”(Analysis Setup) 对话框中选择一个分析,然后单击“分析结果”(Analysis Results) 和“X-Y 坐标图”(X-Y Plot) 组中的选项。此外,可使用“结果诊断”(Results Advisor) 对话框查看分析中发现的问题。单击问题可查看建议的解决方案。
8.生成报告输出。可以使用分析的详细信息以 Microsoft PowerPoint (.ppt) 和 HTML 格式生成报告。
支持的单位制:
以下与材料库相关的对话框仅支持公制单位:
•“材料设置”(Material Setup)
•“冷却时间指示符”(Cooling Time Indicator)
•“分析监视器”(Analysis Monitor)
“浇口设置”(Gate Setup)、“分析设置”(Analysis Setup) 和“分析结果”(Analysis Results) 对话框支持单位转换。
但是,请使用毫米、厘米或英寸作为长度单位,以免出现截断错误。
要打开分析文件:
1.在“应用程序”(Applications) 选项卡中,单击 “模具分析”(Mold Analysis)。“模具分析”(Mold Analysis) 选项卡将显示在功能区中。
2.单击“模具分析”(Mold Analysis) 选项卡。
3.单击 “Mold Analysis 文件 (Mold Analysis File)”,然后单击 “检索项目”(Retrieve Project)。“文件打开”(File Open) 对话框打开。
4.选择 .xedz 分析文件。
5.单击“打开”(Open)。程序打开 CMA 项目时,将显示进度条。
要保存分析文件:
单击 “Mold Analysis 文件 (Mold Analysis File)” 旁的箭头,然后单击以下选项之一保存分析结果:
•“保存项目”(Save Project) - 保存分析结果。默认情况下,结果将保存在工作目录中。
•“另存为项目”(Save As Project) - 将分析结果保存至其他文件夹。
分析结果将保存为 XDEZ 格式。结果文件中可能包含多个分析。
3.关于材料设置
关于材料设置:
必须在执行模具分析前选择材料。单击 “材料设置”(Material Setup),从“材料设置”(Material Setup) 对话框中选择一种塑性材料。“材料库”(Material library) 将按类型、生产商和等级名称列出聚合物。选择材料后,材料细节将显示在“聚合物特性”(Polymer properties) 的以下选项卡中:
•“物理特性”(Physical properties) - 显示选定材料的加工条件。
•“机械特性”(Mechanical properties) - 显示机械特性,包括泊松比、弹性模量和线性热膨胀系数 (CLTE)。
•“黏度”(Viscosity) - 显示“黏度-剪切速率”图。
•PVT - 显示不同压力下的“体积-温度”图。
如果无法找到合适的材料,请编辑现有材料的属性。可使用“材料编辑器”(Material Editor) 对话框修改加工条件、黏度模型和 PVT 模型。
要选择材料:
1.单击 “材料设置”(Material Setup)。随即显示“材料设置”(Material Setup) 对话框。
2.在“类型和生产商”(Type and producer) 下选择一种材料。
3.单击 以展开材料并查看各个生产商。选定材料的可用等级列于“等级名称”(Grade name) 下。
4.从“等级名称”(Grade name) 中选择一个等级。“聚合物特性”(Polymer properties) 部分显示选定等级的物理属性、机械属性、黏度和 PVT 图。
5.单击“确定”(OK) 确认选择。
编辑材料:
单击 “材料设置”(Material Setup) 以查看可用聚合物。如果无法找到所需材料,请按如下方式自定义现有材料的属性:
1.在“材料库”(Material library) 下选择一种材料,然后单击“自定义”(Custom)。“材料编辑器”(Material Editor) 对话框随即打开,且选定材料已列在“自定义材料”(Custom material) 选项卡的“自定义”(Custom) 下。或者,单击“自定义材料”(Custom material) 下的一种材料,然后单击“编辑”(Edit)。
2.请在“物理特性”(Physical properties) 选项卡中提供以下选项的值:
◦“材料”(Material) - 从“材料”(Material) 下拉列表中选择一种材料。
◦“生产商”(Producer) - 键入生产商的名称。
◦“等级名称”(Grade name) - 键入材料等级名称。
◦“熔体温度”(Melt temperature) - 单击并编辑熔体温度的最小值、常规值和最大值。
◦“模具温度”(Mold Temperature) - 单击并编辑模具温度的最小值、常规值和最大值。
PS:必须使用从实验中获得的温度范围。不要使用通过外插法或其他数学方法获得的温度范围。
◦“顶出温度”(Ejection temperature) - 单击并编辑顶出温度值。
◦“固化温度”(Freeze temperature) - 单击并编辑固化温度值。
3.在“黏度”(Viscosity) 选项卡的“黏度模型”(Viscosity model) 下拉列表中选择黏度模型。单击以修改表中的参数值。
4.在PVT 选项卡的 PVT 下拉列表中,选择“压力-体积-温度”模型。单击以修改表中的参数值。
5.单击“确定”(OK)。将出现确认消息。
6.单击“确定”(OK) 确认所做设置。
要导出和导入材料:
在“自定义材料”(Custom material) 选项卡中,选择“自定义”(Custom) 下列出的材料,然后单击“导出”(Export)。将以指定路径将材料另存为 .mtz 文件。
在“自定义材料”(Custom material) 选项卡上,单击“导入”(Import),然后浏览至要导入的 .mtz 文件。输入文件可以包含一个或多个材料。如果存在多个具有相同名称的材料,可以添加备注进行标识。
关于加工条件:
执行分析前,必须设置以下加工条件:
•“填充时间”(Filling time) - 使用塑料熔体填充型腔所需的时间。如增加填充时间,则流动速率和注射压力将减小。
•“熔体温度”(Melt temperature) - 塑料熔体从浇口注入时的温度。熔体温度高将增加流动性,但熔体将需要更长的时间才能冷却至顶出温度。
•“模具温度”(Mold temperature) - 模具温度是模具两个部分的温度。在注射成型过程中,模具温度低于熔体温度。当塑料熔体到达型腔壁时,这有助于型腔曲面实体化。
•“最大注射压力”(Maximum injection pressure) - 最大注射压力是机床能够提供的最大压力。最大注射压力较低将增加短射的可能性。
如果使用的是自定义材料,则必须为以下加工条件指定一个值或使用其默认值:
•“顶出温度”(Ejection temperature) - 该值对估计冷却时间至关重要。顶出温度应高于模具温度 (如低于模具温度,则塑料将为固体)。根据所采用的冷却机构,将持续进行热传递,直到模具温度等于顶出温度,之后再顶出铸模零件。零件的硬度应足以承受顶出系统中零件的局部受力,从而使零件成功顶出。
•“固化温度”(Freeze temperature) - 熔化的塑料变成固体零件。这是一个物理属性,会因材料的不同而不同。
聚合物特性:
黏度模型
黏度用于度量流体流动时的阻力。简单流体 (例如,水和油) 的黏度通常为恒温下的某个常数值。这些流体称作牛顿流体。与简单流体不同,热塑性材料的黏度取决于其化学结构、成份和处理条件。在特定的化学结构和构成下,热塑性材料的黏度取决于温度、剪切速率和压力。
PVT 模型
热塑性材料的体积将随着温度和压力的变化而发生显著变化。因此,非常有必要描述“压力-体积-温度”(PVT) 的关系,以在注射成型分析过程中计算材料的可压缩性。良好的 PVT 模型将描述特定体积与温度和压力之间的相关性。
关于冷却时间指示符:
可估计将零件冷却至填充结束时顶出温度所需的时间。“冷却时间指示符”(Cooling Time Indicator) 对话框将显示估计的冷却时间。运行分析前,可基于估计的冷却时间修改分析设置。
选择材料并单击“分析设置”(Analysis Setup) 溢出菜单中的 “冷却时间指示符”(Cooling Time Indicator)。系统随即显示“冷却时间指示符”(Cooling Time Indicator) 对话框并使用彩色分布指示估计的冷却时间。
•使用滑块来调整颜色图例的上限与下限。
•单击 + 查看材料信息。对所估计冷却时间的计算取决于材料信息。
通常,区域越厚,所需的冷却时间就越长。可修改零件厚度以减少冷却时间。
4.关于浇口设置
关于浇口设置:
浇口为聚合物的注入位置。对于模具型腔内的流动模式而言,浇口至关重要。正确放置浇口可避免大多数缺陷,例如,困气、迟滞、流动不平衡、短射和熔接痕。确定浇口位置后,可使用“长厚比例”(L/t Indicator) 检查浇口布局是否适当。不管浇口直径或模型尺寸进行何种更改,浇口大小始终保持不变。
PS:只能在默认实体主体上添加浇口。不能在构造主体或空主体上添加浇口。浇口位置仅能应用于实体几何曲面,但钣金件除外。
手动添加浇口:
1.单击 “浇口设置”(Gate Setup)。随即显示“浇口设置”(Gate Setup) 对话框。
2.单击“添加”(Add),然后单击默认实体主体的曲面上的位置或基准点以分配浇口位置。随即显示“浇口直径设置”(Gate Diameter Setting) 对话框。
3.在“直径”(diameter) 框中输入浇口直径值。
4.单击“确定”(OK) 关闭“浇口直径设置”(Gate Diameter Setting) 对话框。浇口位置将显示在“浇口设置”(Gate Setup) 对话框中。
5.单击“确定”(OK)。
自动添加浇口:
1.单击 “浇口设置”(Gate Setup) 旁的箭头,然后选择 “自动化浇口创建”(Automatic Gate Creation)。随即显示“自动化浇口创建”(Automatic Gate Creation) 对话框。
2.选择参考坐标系。
如果未指定参考坐标系,将使用默认坐标系来计算浇口位置。
3.从“拖拉方向”(Pull direction) 下拉列表中选择模具开模的方向。
4.在“浇口直径”(Gate diameter) 框中输入浇口直径的值。
5.从“浇口数”(Number of gates) 下拉列表中选择浇口数目。
6.单击“计算”(Calculate) 计算浇口位置。
7.单击“确定”(OK) 将浇口应用至默认实体主体,或单击“关闭”(Close) 以取消浇口位置。自动浇口创建过程将移除默认实体主体上所有先前定义的浇口。
PS:垂直于各自的位置创建浇口。如果浇口方向与浇口位置不垂直,则将浇口旋转至垂直于浇口位置的方向。
要编辑或删除浇口:
1.单击 “浇口设置”(Gate Setup)。随即显示“浇口设置”(Gate Setup) 对话框。
2.从列表中选择一种浇口。
3.执行下列操作:
◦修改浇口直径
a.单击“编辑”(Edit)。随即显示“浇口直径设置”(Gate Diameter Setting) 对话框。
b.在“直径”(Diameter) 框中修改浇口直径值。
c.单击“确定”(OK)。
◦删除浇口 - 单击“删除”(Delete) 以删除选定浇口。
关于长度与厚度指示器:
使用 “长厚比例”(L/t Indicator) 基于现有浇口位置查看流动长度与壁厚的比率分布情况。
设置浇口位置并单击“分析设置”(Analysis Setup) 溢出菜单中的“长厚比例”(L/t Indicator)。随即将显示“长厚比例”(L/t Indicator) 对话框。系统将在图形窗口中使用颜色分布来显示结果。使用滑块来调整显示范围的上限与下限。
最小化长厚比率会减小注射压力和锁模力。可通过添加额外的浇口或更改浇口位置来降低此比率。必须确保长厚比率低于 100。
5.设置和运行分析
设置和运行分析:
在设置模具分析之前,请确保已设置材料位置和浇口位置。
1.单击 “分析”(Analysis)。随即显示“分析设置”(Analysis Setup) 对话框。“材料信息”(Material information) 中将列出材料类型、生产商和等级名称。
2.为“加工条件”(Process condition) 下的以下每项内容输入一个值或使用默认值:
◦“填充时间”(Filling time)
◦“熔体温度”(Melt temperature)
◦“模具温度”(Mold temperature)
◦“最大注射压力”(Maximum injection pressure)
3.如果需要,请在“可选仿真”(Optional simulations) 下选中以下复选框:
◦“计算最大冷却时间”(Calculate maximum cooling time)
◦“计算缩痕”(Calculate sink mark)
◦“计算纤维方向”(Calculate fiber orientation)
4.拖动“网格元素大小”(Mesh element size) 滑块选择网格元素大小。
◦“粗糙”(Coarse) - 建议用于快速填充分析。此设置将生成较少的网格元素,因此需要的计算时间更少。结果的准确性将降低。
◦“精细”(Fine) - 建议用于标准机械零件的常规模拟。此设置将以更高的分辨率生成实体网格元素,并使用常规设置执行分析。
◦“精度”(Accuracy) - 建议用于获取所有零件的深度分析。此设置将生成更精细的网格,并更准确地执行分析。需要的计算时间更长。
5.单击“添加”(Add) 以添加多个运行。可以使用各种浇口位置、加工条件以及用于分析的网格级别来设置多个运行。
PS:仅对已定义了浇口的默认实体主体运行分析。在“分析设置”(Analysis Setup) 对话框启用时,您可以在模型树中更改默认主体,并添加新的分析运行。不能在构造主体或空主体上创建分析。
6.选择分析,然后单击“激活”(Activate) 可修改加工条件、可选仿真和网格元素大小。单击“应用”(Apply) 以保存更改。
7.如果要重命名分析或向其中添加备注,请双击该名称,然后在“编辑名称”(Edit Name) 对话框中添加详细信息。单击“确定”(OK)。备注将显示在“名称”(Name) 列下。
8.选择分析,然后单击“移除”(Remove) 可将其从分析中移除。
9.选中要执行分析的运行所对应的复选框,然后单击“运行分析”(Run Analysis)。“分析监视器”(Analysis Monitor) 对话框将显示分析详细信息,包括加工条件、材料信息、模型信息和分析日志。此监视器还将显示进度百分比和完成分析的剩余时间。
PS:单击“运行分析”(Run Analysis) 之前,必须至少选择一个运行。如果修改运行的加工条件或重新计算运行,则本次结果将覆盖上次结果。
在系统上安装 IntelMPI 以使用并行计算执行更快速的分析。有关安装 IntelMPI 的详细信息,请参阅《PTC Creo 安装与管理指南》。
要选择分析:
完成分析后,可选择要查看其结果的分析。
1.单击 “分析”(Analysis)。随即显示“分析设置”(Analysis Setup) 对话框。
2.单击列表中的某个分析,然后单击“激活”(Activate)。选定分析的详细信息随即显示。
3.如果要重命名分析或向其中添加备注,请双击该名称,然后在“编辑名称”(Edit Name) 对话框中添加详细信息。单击“确定”(OK)。备注将显示在“名称”(Name) 列下。
4.如果要检查分析的详细信息,请单击鼠标右键并选择“显示分析日志”(Show analysis log)。分析日志窗口会显示加工条件、模型信息以及填充阶段的数据。
5.单击“关闭”(Close)。
选择分析结果后,可使用各种工具显示和解释分析结果,例如,“X-Y 图”(X-Y Plot)、“视图控制”(View Control)、“动画”(Animation) 和“结果诊断”(Results Advisor)。
二.模流分析结果
1.关于查看结果
关于查看结果:
可使用以下选项使注射成型分析结果可视化并对其进行解释:
•“分析结果”(Analysis Results) 选项 -“分析结果”(Analysis Results) 组中包含多个结果选项,例如,“成型性”(Moldability)、“熔体前沿时间”(Melt Front Time)、“困气”(Air Trap) 和“熔接痕”(Weld Line)。单击各个选项可分别对结果进行分析。结果将以颜色分布加以显示。
•“X-Y 坐标图”(X-Y Plot) 选项 - 单击“X-Y 坐标图”(X-Y Plot) 组中的某个选项以观察注射成型过程中相对于时间的物理变化。可以分析主流道压力图、锁模力图和流动速率图。
•“结果诊断”(Results Advisor) 对话框 - 单击“结果诊断”(Results Advisor) 以查看在分析中发现的潜在问题。“结果诊断”(Results Advisor) 对话框中包含检测到的失败的解决方法链接。
•“视图控制”(View Control) 对话框 - 使用“视图控制”(View Control) 对话框中的功能可查看内部变化情况。可以动画显示流动模式,且其播放速度和帧步长均可调。
要查看结果:
•要查看模型的颜色分布结果,请执行以下操作:
a.从“分析设置”(Analysis Setup) 对话框中选择一个分析并激活。
b.在“分析结果”(Analysis Results) 组中单击以下选项之一:
▪“成型性”(Moldability)
▪“熔体前沿时间”(Melt Front Time)
▪“困气”(Air Trap)
▪“熔接痕”(Weld Line)
▪“缩痕”(Sink Mark)
▪“压力”(Pressure)
▪“温度”(Temperature)
▪“中心温度”(Center Temperature)
▪“体表温度”(Bulk Temperature)
▪“最大剪切速率”(Maximum Shear Rate)
▪“最大剪应力”(Maximum Shear Stress)
▪“固化层比例”(Frozen Layer Ratio)
▪“最大冷却时间”(Maximum Cooling Time)
▪“速度矢量”(Velocity Vector)
▪“体积收缩”(Volumetric Shrinkage)
▪“浇口贡献”(Gate Contribution)
▪“材料方向”(Material Orientation)
结果在图形窗口中将显示为颜色分布。
c.再次单击该选项可隐藏颜色分布结果。
•要查看模型的 X-Y 图结果,请执行以下操作:
a.选择并激活要查看其结果的分析。
b.在“X-Y 坐标图”(X-Y Plot) 组中单击以下选项之一:
▪“主流道压力”(Sprue Pressure)
▪“锁模力”(Clamping Force)
▪“流动速率”(Flow Rate)
相应结果的曲线将显示在图形窗口中。
c.再次单击该选项可隐藏 X-Y 图。
要使用视图控制选项查看结果:
1.从“分析设置”(Analysis Setup) 对话框中选择一个分析并激活。
2.在“分析结果”(Analysis Results) 组中单击一个结果选项,然后单击 “视图控制”(View Control)。随即显示“视图控制”(View Control) 对话框。
3.使用“视图控制”(View Control) 中的函数以不同的表示查看结果:
◦“截面”(Section) 选项卡 - 选择以下其中一个截面视图选项以查看内部变化。
▪“剪切”(Clipping) - 通过键入方程变量的值定义剪切平面。
▪“层切”(Slicing) - 通过键入方程变量的值定义层切平面。
▪“等位面显示”(Isosurface display) - 显示模型中某个值的等位面。等位面上所有点的结果值均相同。
◦“图例”(Legend) 选项卡 - 调整颜色图例的设置。
◦“动画”(Animation) 选项卡 - 通过使用动画检查流动模式。
▪“显示速度”(Display speed) - 调整滑块以提高或减慢动画播放速度。
▪“显示步骤”(Display step) - 调整值的大小以扩大或减少每帧的步长百分比。
▪“当前步骤”(Current step) - 调整值的大小以查看特定时刻的结果。
▪“播放”(Play) - 单击
播放动画。当前步长会自动同时发生更改。
▪“暂停”(Pause) - 单击
即刻停止动画。
▪“停止”(Stop) - 单击
在填充过程结束时停止动画。
PS:选项的可用性取决于选择的结果。
4.单击“关闭”(Close),关闭对话框。
要生成报告:
生成报告之前,请从“分析设置”(Analysis Setup) 对话框 (“模具分析”(Mold Analysis) > “分析”(Analysis)) 中选择要创建报告的分析。
1.单击 “生成报告”(Generate Report)。随即显示“创建报告”(Create Report) 对话框。
2.[可选] 在“报告信息”(Report information) 下,输入需要在输出报告中使用的信息。可输入细节,例如报告标题、公司名称和公司徽标。
3.在“报告路径”(Report path) 下,单击“浏览”(Browse),然后指定用于保存报告的路径。
4.在“报告类型”(Report type) 下选择报告的格式。
5.如果希望生成的报告包含结果说明,请选中“分析结果说明”(Analysis results description) 复选框。
6.单击“确定”(OK) 生成报告。将在指定位置将报告另存为 Microsoft PowerPoint (.pptx) 或 HTML 文件。
2.关于结果诊断
关于结果诊断:
单击 “结果诊断”(Results Advisor) 查看在分析中发现的问题。“结果诊断”(Results Advisor) 对话框将显示以下内容:
“发现的问题”(Found Issues) - 将列出执行模具分析时发现的问题。单击某个失败以查看其说明、解决方案和动画。
“问题说明”(Problem Description) - 将显示选定问题的说明。
“预览”(Preview) - 将显示选定失败的动画。
“建议解决方案”(Suggested Solutions) - 将显示选定失败的相应解决方法。
依照解决方法中建议的方式更新分析,然后重新运行分析。
关于模具分析结果:
结果
|
说明
|
---|---|
成型性
|
成型性结果将显示在常规注射成型条件下在型腔区域中填充塑料熔体的容易程度。
良好 – 熔体将完全填充区域。熔体前沿温度远高于固化温度。
中 – 熔体可能很难填充区域且零件可能会存在质量问题。熔体前沿温度略高于固化温度。
低 – 熔体很难填充区域且零件可能会存在质量问题。熔体前沿温度接近固化温度。
|
熔体前沿时间
|
“熔体前沿时间”结果将显示填充过程中相对于时间的流动模式。
|
困气
|
困气结果将显示可能会产生困气的位置。熔体前沿因聚集会形成小气泡,从而产生困气。它可能会出现在型腔内的多个位置。
|
熔接痕
|
熔接痕结果将显示指示较弱结构的潜在点的熔接痕。熔接痕越深,结构就越不稳固。
|
缩痕
|
缩痕是铸模零件曲面上的凹陷。尽管缩痕不影响零件的强度或功能,但被认为是严重的质量缺陷。在冷却过程中,收缩产生的内压导致内部塑料收缩和实体化曲面层变形时,将会出现缩痕。
缩痕结果将显示整个型腔曲面内可能的缩痕位移。较高的值表示收缩程度大。可通过减小填充时间来补偿塑料收缩,从而消除缩痕。
|
压力
|
压力结果将显示填充结束时塑料的压力分布情况。
|
温度
|
温度结果将显示填充结束时塑料的温度分布情况。
|
最大剪切速率
|
该结果将显示填充过程中记录的每个元素的剪切速率峰值。
剪切速率是指加工聚合物时材料的剪切变形速率。剪切速率分布与速度梯度和分子取向的变化相关。剪切速率高容易导致分子链严重变形。甚至能使零件发生断裂和降低零件的强度。应观察因剪切速率高而导致的粘性温度升高情况。
|
最大剪应力
|
该结果将显示填充过程中记录的每个元素的剪应力峰值。
可使用该结果来确定成品零件的最大剪应力是否超出了允许的最大剪应力。
|
固化层比例
|
“固化层比例”结果将显示填充结束时,固化塑料相对于零件厚度的体积百分比。
|
最大冷却时间
|
该结果将显示零件厚度方向上的最大冷却时间。这是基于填充结果得出的估计值。该值将为模具设计的冷却槽布局提供一些参考。
|
速度矢量
|
速度矢量结果将显示填充结束时塑料熔体的速度矢量。
|
体积收缩
|
体积收缩结果将显示当填充结束后,零件从高温高压冷却至环境温度和环境压力下时,零件体积百分比变化的分布情况。
|
浇口贡献
|
浇口贡献结果将显示填充结束时每个浇口的注入塑料熔体的体积贡献度。结果值为百分比形式。要获得经过优化的结果,需要获得平衡的浇口贡献
|
“纤维方向”
|
纤维方向结果可显示塑料熔体内的方向分布。
|
材料方向
|
材料方向结果将显示塑料熔体的方向矢量分布情况。
|
主流道压力图
|
主流道压力图是主流道压力相对于填充时间的图形。
|
锁模力图
|
锁模力图是锁模力相对于填充时间的图形。
|
流动速率图
|
流动速率图是所有浇口的流动速率之和相对于填充时间的曲线图。
|
熔体前沿时间结果:
应多加注意熔体前沿时间结果的颜色梯度。如果某一区域的颜色发生了巨大变化,则表示该区域的流动速度低于其他区域。经过优化的“熔体前沿时间”结果将显示每个浇口的平衡流动贡献度。所有随动路径均同时到达型腔壁。可从“熔体前沿时间”结果中发现以下问题:
•迟滞 - 如果区域中的颜色发生巨大变化,则表示型腔中的流动速度低,从而导致了流动迟滞。在极端情况下,迟滞可能导致零件曲面出现迟滞痕迹,甚至会造成短射。
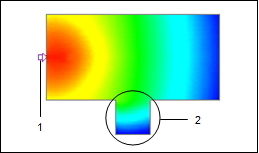
1.浇口
2.迟滞区域
•熔接痕 - 在填充过程中,当两个不同的熔体前沿呈锐角形式的连接时,将形成熔接痕。熔接痕可降低成品的强度并产生曲面缺陷。
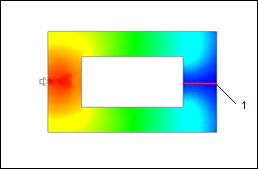
1.熔接痕
•困气 - 困气由可形成小气泡的熔体前沿聚集而成。它可能会出现在型腔内的多个位置。
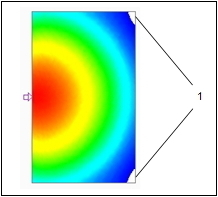
1.困气
•短射 - 模型在填充结束时填充不完全可能会导致短射。
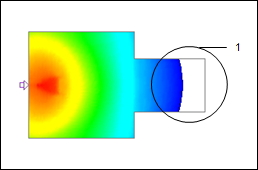
1.短射
•过保压 - 某些随动路径先于其他路径填充完全。继续使用额外塑料熔体填充这些填充的随动路径,直到整个型腔填充完全。随动路径填充过满的条件称为过保压。
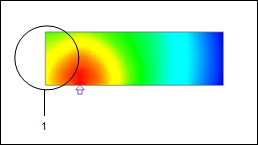
1.过保压区域
•跑道效应 - 塑料熔体以不同的速度在每条随动路径上移动。壁较厚区域的流动阻力低于壁较薄区域的流动阻力,因此,熔体在壁较厚区域的流速会更快。如果随动路径较长,则较薄区域可能会出现熔体回填的情况。回填可能会导致困气和熔接痕。下图显示了跑道效应。主视图显示了熔体前沿的速度差异。侧视图显示了模型的厚度分布。
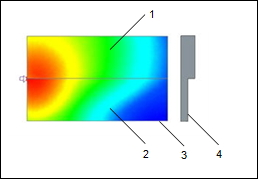
1.流动阻力较小区域
2.流动阻力较大区域
3.主视图
4.侧视图
压力结果:
压力结果将显示填充结束时塑料的压力分布情况。可借助压力结果来确定以下注射成型问题:
•短射 - 应分析压力传递条件。型腔厚度会限制注射压力向型腔中的传递。注射压力将驱动塑料熔体,减小型腔厚度可能会导致短射。
•过保压 - 可通过分析熔体前沿时间和压力结果更精确地预测过保压。过保压主要由流动不平衡所致,可通过“熔体前沿时间”结果进行观察。如果流动不平衡,请检查早期填充的随动路径中的压力是否过高以确定过保压。
可修改设计或分析设置以修复成型方面的问题。
温度结果:
温度结果将显示填充结束时塑料的温度分布情况。可借助温度结果发现以下问题:
•确定高摩擦生热区域 - 浇口附近和厚度较小区域的流动阻力将变得非常高。流动阻力较大将导致塑料熔体的摩擦生热。应借助温度结果检查浇口和厚度较小区域附近是否出现任何温度升高现象。
•请检查温度变化是否与加工条件和设计中的更改相对应 - 可修改产品设计或加工条件以获得优化结果。因此,如果更改壁厚,则温度分布将会更改,因为较厚的型腔很难向模具中散热。
可修改设计或分析设置以修复成型方面的问题。
中心温度结果
中心温度结果将显示填充结束时沿厚度方向中间层的熔体温度。中心温度是传递给新热熔体的热能的指示器。如果中心温度过低,则会发生流动迟滞,此现象可导致短射问题。
体表温度结果
体表温度是在填充过程结束时沿厚度方向的速度加权平均熔体温度。计算体表温度 (T体表) 的方程如下:
假设模型厚度的方向为
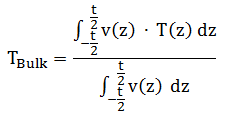
其中 t 为模型的厚度,v 为熔体的速度,T 为熔体的温度。
结果将忽略固化层的温度贡献。可从此结果中观察热对流和粘滞发热的效果。体表温度将显示热对流对迟滞和粘滞发热区域温度分布的效果。
体表温度分布将反映随动路径的趋势,因此也将反映压力传递的实际路径。
固化层比例结果:
固化层比例是型腔侧与型芯侧的固化层厚度与零件厚度之比。“固化层比例”结果将显示填充结束时,固化塑料相对于零件厚度的体积百分比。随着零件的实体化,该值逐步变为 100。
由于实体化 (由冷却所导致),将在型腔曲面附近形成固化层。固化塑料厚度的增大将减小沿随动路径的横截面的面积,因此将增大流动阻力和主流道压力。
较厚的固化层可降低形成缩痕的几率,但是会增大形成空洞的几率,因为实体化塑料较难变形。固化层比例也将影响残余应力和流动方向。
体积收缩结果:
体积收缩结果将显示当填充结束后,零件从高温高压冷却至环境温度和环境压力下时,零件体积百分比变化的分布情况。对体积收缩的计算基于塑性材料的 PVT 关系。
正值表示体积收缩,而负值表示体积膨胀。较大的正值表示体积收缩大,这可能会导致缩痕或空洞。在理想条件下,需要获得均匀的体积收缩。获得均匀的体积收缩要比较小的体积收缩量更为重要。
以下为导致体积收缩不均匀的原因:
•非均匀压力分布
•非均匀温度分布
体积收缩不均匀可导致以下问题:
•零件顶出后出现翘曲。
•如果应力无法转换为变形,则会因产生热量而导致出现残余应力。
X-Y 图结果:
主流道压力图
主流道压力图是主流道压力相对于填充时间的图形。可借助此图来发现填充过程中主流道压力的异常增大情况。通常,主流道压力不会超过被设置为加工条件的最大允许注射压力。如果计算的主流道压力在填充结束前,持续上升到最大允许注射压力,则可能会产生迟滞或短射。
锁模力图
锁模力图是锁模力相对于填充时间的图形。锁模力是确保模具的两部分紧压在一起所需的力。可借助此结果来发现毛边问题。如果计算的锁模力大于机床最大锁模力的 70%,则塑料熔体就有可能被挤出型腔,进而导致出现飞边。
流动速率图
流动速率图是所有浇口的流动速率之和相对于填充时间的图形。如果达到最大值,则流动速率不会增加。